Understanding Electric Vehicle Motor Controllers: A Beginner's Guide
The electric vehicle (EV) industry has been snowballing lately. If you’re interested in electric vehicles and motor control systems, you have come to the right place. This article will provide information on Motor Control in Electric vehicles and motor controller operations.
Anticipating CY2030, worldwide EV sales are supposed to reach 47.8 million, representing around 50% of new passenger vehicles sold. Worldwide deals of EVs have arrived at 6.7 million. China’s EV deal volume was 3.33 million units in CY2021, and surpassing 6 million units in CY2022 is normal.
EVs need more electric engines than conventional vehicles because of multiple factors. They must supplant belt or wrench/cam shaft-driven extras like siphons, blowers, and actuators. They also need engines for new frameworks, such as electronic control coolant siphons. While EVs could use brushed DC (BDC) engines, Brushless DC (BLDC) engines provide essential benefits for EVs:
- Better energy proficiency
- Quieter activity utilizing sinusoidal control
- Improved reliability and delayed engine life
Taking vehicle electronic water pumps as an example, an EV requires more than a standard ignition motor vehicle. An EV must carry out temperature controls for three new frameworks:
- The high-voltage battery pack
- The foothold engines
- The footing engine inverter electronic control sheets
A typical set of three electronic water siphons is required per EV, and the cost of an electronic water siphon is higher than that of a traditional belt-driven mechanical pump.
GET THE COURSE: Electric Vehicle Design Simulation and Component Selection
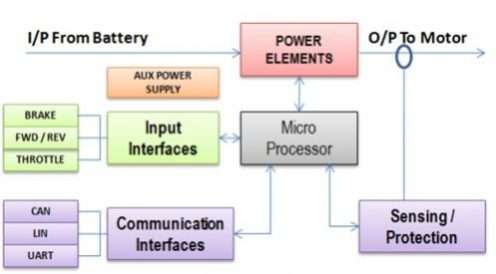
Purpose of Motor Controller in EV
An electric vehicle motor controller combines power electronics and embedded microcomputers that effectively convert the energy stored in the batteries into motion.
A simplified block diagram of a typical electric three-wheeler vehicle can be seen on the cover. As one can see, the motor controller is the main element that regulates the energy supply to the motor.
The motor controller receives commands from interfaces such as the throttle, brake, and forward/reverse control switches. The motor controller processes these commands and very precisely controls the speed, torque, direction, and consequent horsepower of a motor in the vehicle.
Motor controllers can reverse the energy from the motor and transfer it from the battery to the motor to accelerate the vehicle’s return to the battery, which gives electric vehicles a more effective braking system than a standard mechanical brake system.
This feature, often known as “regenerative braking,” also enhances the vehicle’s range by recharging batteries each time an electric car brakes.
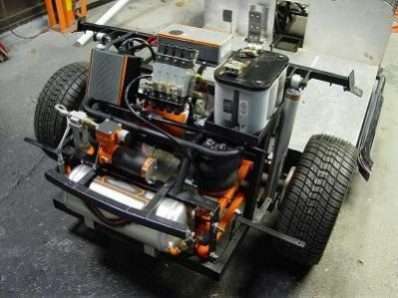
Motor Controller’s Operations
The system’s brain is a microprocessor with embedded firmware that enables all of the motor controller’s operations.
- The power electronics section, or power elements block, is a bi-directional power converter. It can move energy from the battery to the motor and vice versa.
- The input interface block connects to the motor controller and the other vehicle components.
- The direction of future transportation is toward shared and autonomous cars. One of the essential components of the motor control unit is the communication block, which allows the motor controller to share data with external systems. A motor controller can transmit data and receive instructions through a communication block.
- Motor controllers and electric power trains are better candidates for shared and autonomous mobility since they can share data and synchronize with external systems in real-time.
All system characteristics, including battery voltage, current, motor speed, voltage, and current, are measured by the sensing/protection block.
The motor controller carefully monitors and precisely regulates each of these variables. The system will initiate self-protection if a malfunction is found, safeguarding the safety of the vehicle and its occupants.
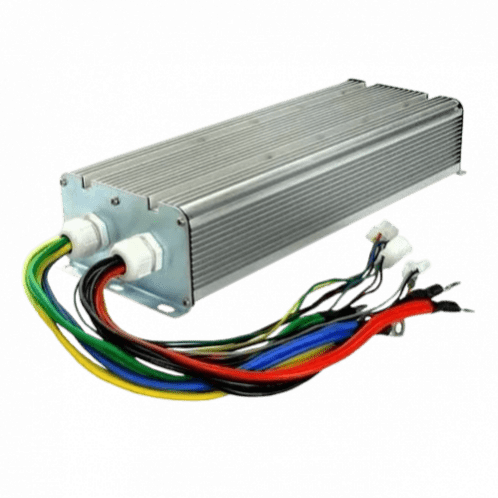
Controllers a Challenge in India
It is well known that foreign motor controllers make up the bulk of those utilized in India.
The following are difficulties with Indian controller production.
- Electric Vehicle should note that Indian motor firms have historically produced induction and brushed DC motors, which Do not require controllers.
- Therefore, the market’s need for controllers is very recent. For several application areas, including EVs and inverter technology for air conditioners and refrigerators, BLDC motors have only recently been launched.
- Another factor is a need for more organizational and individual technical capability. Most importantly, manufacturing motor controllers requires expertise in electrical machines, embedded systems, power electronics, and control systems.
- Semi-conductive devices are a fundamental part of a motor controller; however, there needs to be more curricula and opportunities for people to practice these abilities.
- Although they are not made in India, a good supply chain exists that imports semiconductors and provides them to Indian businesses.
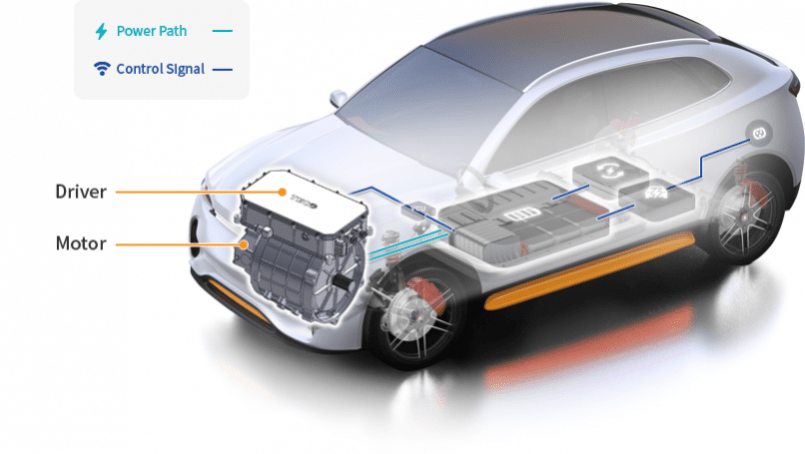