Increasing Silicon in EV Batteries: Challenges and a Potential Solution
The race to develop and sell new electric vehicles (EVs) is driving huge investments in new battery materials; new cell manufacturing process technologies; and new factories in key markets. In fact, The International Energy Agency predicts that by 2040, 55% of all new car sales and 33% of the global fleet will be electric.
The battery advances we read about today focus on cathode chemistries; solid electrolytes; and the vertical integration and localization of EV battery supply chains by EV makers to increase and diversify production capacity while decreasing production costs.
As consumers continue to demand better, more affordable EVs, one manufacturing process is gaining significant traction – adding more silicon onto the battery. To better understand the end-user benefits, it’s important to review the near- and long-term impact of silicon on developing better EV batteries.
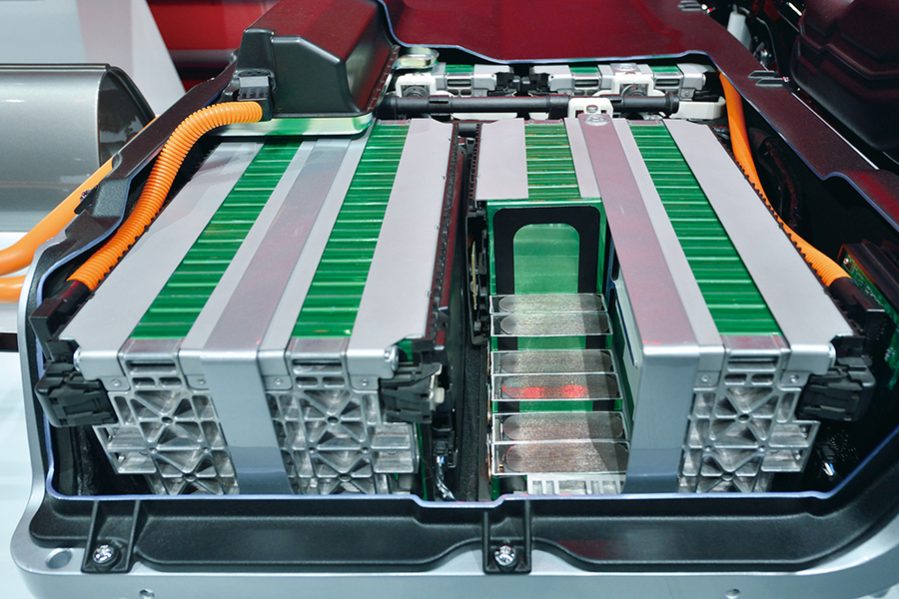
The Role Of Silicon In Developing better EV Batteries
Somewhere around two driving EVs currently incorporate silicon added substances blended in with graphite in the anode, to offer longer reach and quicker charging: the Tesla Y and the Porsche Taycan. Industry specialists predict that in the following couple of years, how much silicon in the EV anodes and the quantity of EVs with silicon- graphite anodes will both increment. It is the main practical method for expanding the anode energy thickness furthermore, charging speed while also decreasing anode expenses and carbon impression. In a couple of years, EVs without silicon in the battery will turn out to be progressively out of date.
Today, EV organizations presently can’t seem to choose the most effective way to add more silicon. As vehicle producers also, cell producers rush to an answer, it’s essential to inspect the obstacles that to date, have prevented versatile arrangements.
Challenges with adding Silicon to Anode
-
The inclination of silicon particles to break during cycling: It is deep rooted that particles more noteworthy than 200 nm effectively crack when silicon compounds with lithium, which causes huge volume changes.The ongoing arrangement – currently involved today in a few existing EVs – is to add oxygen molecules and use micron-sized silicon oxide particles: the oxygen molecules structure bonds that keep intact the silicon particles. Tragically, this arrangement is costly and restricted. Silicon oxide added substances increment the first cycle misfortune (and accordingly the cathode cost) and decline the silicon reversible limit and they can’t be utilized to additional increment current silicon stacking.
-
The silicon surface consumes too much electrolyte to form a SEI (solid electrolyte interface): This is most apparent in silicon powders with particles sizes less than 200nm, which exhibit a very high surface area (BET). Various solutions have been proposed, from carbon-coatings to amorphous carbon shells and conductive polymer matrices. All these solutions have three common drawbacks: increased inactive materials; increased costs; and lack of scalability. The lack of scalability can be traced to the difficulty producing and mixing large quantities of these new silicon additives to EV- grade graphite powders produced by multiple suppliers and achieving uniform anode coatings in existing large EV cell factories.
-
Silicon fragments become electrically isolated during long cycling, thus trapping lithium ions and decreasing battery life, especially at higher silicon loadings: Various solutions have been tested, from adding carbon nanotubes and specialized polymers to mixing silicon nanoparticles within graphene flakes and forming secondary composite particles. These solutions are highly dependent on the specific slurry composition, preparation and coating techniques of each EV cell maker, which are typically well-guarded trade secrets, and are not compatible with the broad range of synthetic and natural graphite powders available from the leading suppliers in key markets.
So what is the Solution?
The business needs a method for wedding more silicon with numerous EV-grade business graphite powders, which leads for all intents and purposes no progressions in the anode dynamic material surface region (BET); in the anode slurry planning and covering; in the dynamic to latent materials anode proportion; if the EV cell arrangement convention and in the EV cell cycle life. Enormous scope creation that lessens expenses and carbon impression is additionally an absolute necessity. The method for noting these requests in the following five years is through impeccably molded furthermore, measured silicon nanowires – materials that can significantly increase the energy thickness of the anode while diminishing expenses and carbon impression.
It has become clear that cutthroat powers are driving the need to enhance quicker, to decrease gambles what’s more, to enhance new cell plans that can be created in huge amounts by leveraging numerous providers – developing silicon nanowires straightforwardly onto the particles of EV-grade graphite powders, intertwining the silicon precisely and electrically to the graphite without adding any idle materials also, without expanding the BET surface region. This guarantees that current EV plants can profit from silicon-upgraded graphite from their all around qualified driving providers and can utilize a similar slurry planning and anode cathode it been idealized to cover strategies that have as of now.