The Rise of EVs and the Evolution of Automotive Manufacturing Processes
In the ever-evolving landscape of automotive manufacturing, the past 120 years have seen significant innovations, from Henry Ford’s assembly line to Toyota’s Just-In-Time production. However, a new era is dawning as the automotive industry embraces cutting-edge technologies and shifts towards Electric Vehicles (EVs). This blog explores the transformative impact of technologies like 3D printing, new-age composite materials, modularization, unibody casting, and Assisted Driving Systems (ADAS) on the future of automotive manufacturing.
1. 3D Printing/Manufacturing:
While 3D printing technology was invented in 1980, its true potential is now being realized in automotive manufacturing. Predicted to reach a market valuation of $27.7 billion by 2023, 3D printing is becoming indispensable for prototyping, functional testing, design optimization, and rapid tooling. Notably, Local Motors showcased the world’s first 3D printed electric car, Strati, in 2014, emphasizing the technology’s ability to reduce costs, enhance efficiency, and revolutionize the automotive supply chain
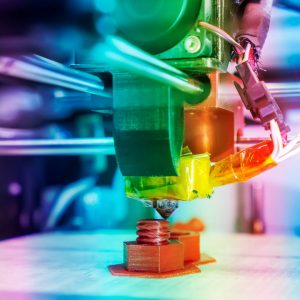
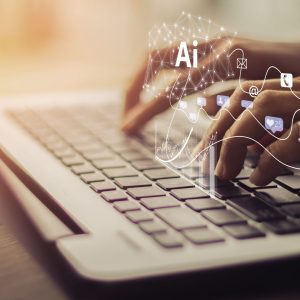
2. Application of New Age Composite Materials:
The automotive industry is experiencing a surge in demand for advanced materials to meet higher fuel efficiency standards. Materials like aluminum, magnesium, and high-performance composites are being utilized to achieve weight reduction without compromising safety. The market for automotive lightweight materials is projected to grow at a CAGR of 7.4% from 2019 to 2027, reaching $157.7 billion. These materials not only enhance fuel efficiency but also contribute to improved safety and recyclability.
3. Modularization in Automobile Manufacturing:
As the industry transitions from Internal Combustion Engine Vehicles (ICEVs) to EVs, about 31% of components and related manufacturing processes will be phased out. Israeli firm REE Automotive is introducing a “skateboard” EV chassis, where wheel units integrate critical vehicle components. This modular approach allows for the creation of various EV platforms, streamlining the manufacturing process and enabling flexibility in vehicle design.
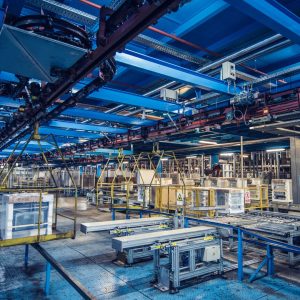
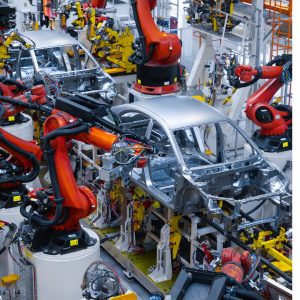
4. Unibody Casting of Body Shell:
Tesla is leading the way in revolutionizing the manufacturing process with its single-piece casting method. Using massive Giga Presses, Tesla aims to produce entire vehicle bodies in one piece, eliminating hundreds of intermediate processes in traditional manufacturing. This method not only reduces production time by 25% but also demonstrates the potential to take automotive manufacturing to the next level.
5. ADAS Supporting Manufacturing:
Assisted Driving Systems (ADAS) are becoming a crucial technology for both EVs and ICEVs. The evolution from Level 2 and 3 ADAS to Level 5 involves a paradigm shift in connectivity and control technology. The advent of Connected and Autonomous Electric Vehicles (CAEVs) is on the horizon, with the ability to autonomously navigate roads. While the manufacturing processes for these futuristic vehicles are still in development, the integration of ADAS into manufacturing is evident, highlighting the industry’s commitment to road safety.
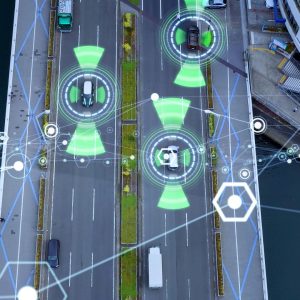
Conclusion:
As the automotive industry undergoes a transformative phase, the rise of Electric Vehicles signals a survival-of-the-fittest battle in manufacturing. The integration of technologies like 3D printing, new-age composite materials, modularization, unibody casting, and ADAS will shape the future of automotive manufacturing. OEMs and their supply chains must navigate uncertainties and prepare for unforeseen challenges in this emerging market. The outcome will reveal the pioneers guiding the next era of automotive manufacturing, akin to the legacies of Henry Ford and Toyota, as the industry settles into the years ahead.